Having regular maintenance performed on your Building Automation System (BAS) equipment is important and necessary.
A regular maintenance schedule will keep your equipment up to date and allow you to better monitor and control your energy usage.
You’ll find that your BAS equipment will have fewer unexpected issues—thereby saving your organization time and money while avoiding costly BAS problems.
Read on to learn more about the benefits of BAS maintenance and what would happen if you didn’t keep your system on a regular maintenance schedule. We'll also examine the different types of maintenance plans and scheduling for building operators.
Why Do You Need BAS Maintenance?
Is BAS maintenance really that important?
Let’s be honest: There is ZERO value to ignoring regular maintenance—aside from the initial and temporary "appearance" of saving money. It will end up costing far more in terms of breakdowns, malfunctions, and system failures if you neglect to keep your system in proper running condition.
Some of the benefits of regular maintenance are:
Increased Energy Efficiency and Reduced Energy Costs
Regular maintenance ensures that your BAS runs as efficiently as possible, thereby reducing utility bills and operating and maintenance costs.
BAS equipment that runs constantly is prone to wear-and-tear, such as minute degradation or malfunctions in parts, gauges, or temperature sensors.
These seemingly "little things” that can go wrong will always add up to higher energy consumption—a sensor here, a controller there.
Reduced Overall Costs
Regular maintenance also ensures that your system runs in optimal condition and can help catch issues before they grow into large problems. This, in turn, reduces the amount of system downtime.
Compare the following:
A maintenance technician catches a "little problem" that can be fixed in 30 minutes and is covered under the plan…
Versus a major equipment breakdown that occurs because you didn’t address that seemingly "little problem.” The equipment breakdown now requires expensive parts shipped in and several days of downtime as the contractor has to install everything and test the system.
Increased Life of the System
Having regular maintenance performed also ensures that you’re getting the most bang for your buck. Neglected or infrequently serviced equipment, such as air conditioning units, go downhill much faster than well-maintained ones.
Maintenance identifies the damage that leads from constant wear and tear and fixes it before it becomes a bigger problem. This can add years to the life of your control systems and equipment.
System Stays Current
When technicians perform maintenance, they make sure to install the latest software and technology. They also implement new safeguards and any other technological changes and improvements.
Improved Indoor Air Quality
In addition to improving building occupant comfort, regularly scheduled BAS maintenance can also help improve the air quality. The sensors and filters of the HVAC system could require replacement or maintenance to ensure they’re working properly.
Depending on your building location and the quality of the outdoor air, there are many different types of indoor pollutants and odorless carcinogens, such as:
- Carbon Dioxide (CO2)
- Carbon Monoxide
- Volatile Organic Compounds (VOCs)
- Formaldehyde
- Nitrogen Dioxide
These pollutants can significantly build up inside a building where the BAS system isn’t running at optimal performance.
What Happens if You Don’t Have Regularly Scheduled Maintenance Visits?
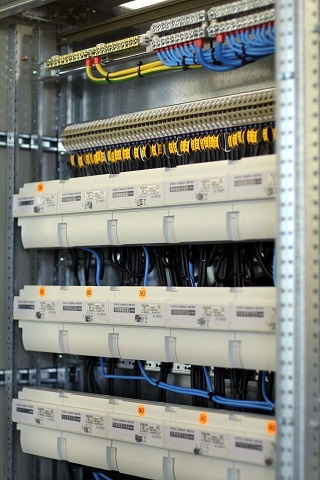
More Severe Equipment Breakdowns
Not taking care of a building automation system opens the door for little issues to creep up and grow into much bigger ones.
That takes much more time, parts, and money to fix. Furthermore, the time that the system is offline for repairs could cause operational downtime at your facility.
Energy Inefficiency and Increased Costs
Any building system that runs constantly will quickly begin to degrade and run inefficiently. There are so many areas in a large, complex system where these problems can set in.
Without regular maintenance, the energy efficiency benefits of a BAS are of little value—which ultimately leads to increased energy costs.
Types of Maintenance Plans
- You can choose a biannual, quarterly, monthly, or daily plan depending upon the size of your BAS and whether it needs to run at peak capacity and efficiency at all times.
- You can choose a yearly or multi-year term contract.
When you get a plan, check to see if it provides after-hours and emergency services, as many do not.
BAS Maintenance is Important
Building automation is integral to the smooth functioning of your organization and will help ensure equipment stays in peak running condition. It’s a wise choice to take advantage of a regular maintenance plan and keep a schedule of frequent checkups. Your BAS, occupants, and bank account will thank you for it.
Contact Mid-Atlantic Controls to learn more about pricing for a BAS maintenance plan for your business.